I don't like Ikea. Don't get me wrong, some of their stuff is great, but when it comes to their non-wood flat-pack furniture made out of that press/chip/particle/fiber/wafer board, I'm not a fan. Sure, it is finished really nicely, but it isn't wood. This "rant" applies to all of the ilk, not just Ikea. I've heard people have good success with things like kitchen cabinets and closets that you build in, and never move. But after a few years go by and moisture gets under the finished surface, or a corner curls, or a screw or two gets loose in a hinge... Well, you get the idea. Don't get me wrong, some of their real wood furniture items really do wear well. However, as most of their furniture is flat-packed (flat case pieces, bags of fasteners and other hardware and a couple simple tools to assemble them with) and made to be assembled without glue or clamps, the joint is usually a mechanical one - the quick / cam metal fasteners are holding the piece together. Nothing wrong with that... ...until you move it. Metal fasteners are stronger than wood and they don't give. Ikea engineers do a pretty good job of making sure that the furniture can resist the stress of normal use, but as soon as something gives a wracking force jolt, the metal hardware will do its best to keep things together, but what ends up "giving" is the MDF / chipboard - it will flake, dent and delaminate if you look at it wrong. And, as soon as a piece starts to get wiggly, it is only going to get worse.
Ok, woodworkers / cabinet makers are not the target audience of flat packed furniture. However, I'm sure I'm not the first that has been roped into assembling one, or been asked to fix after it has started going bad.
I have a couple suggestions:
First, use glue - it isn't going to help as much as if the product was wood, but it will help a lot. Some people think glue and Ikea are a bad combination, but the basic argument is that it makes it take longer to assemble, and you lose the flexibility of being able to break it down later. Well, most folk I know don't move so often that this is an issue. But, something to consider if you are putting something together for a teen or someone college-age.
Second, replace flimsy backs with plywood. A lot of Ikea backs are just for show, not to prevent wracking stress. Some of their backs are only 2mm thick, and are basically finished paper. If you want, you can glue that back to plywood, and then attach it to the case. I got this tip from my friends Don and Sue, who replaced the backs of some of their bookcases many years ago to help make them more earthquake proof / allow them to secure them to the wall.
Third, replace screws with nuts and bolts (not always possible, mostly screws are used for blind-side applications.) Screws strip out. Not all Ikea screws are the nice Spax (shown at left) or Confirmat screws that are made for MDF / particle board. But, when you can, upgrade fasteners. Sometimes the upgrade has to be gluing hinges rather than replacing fasteners. FYI, Spax screws are available at both Lowes and Home Depot & although you still need to pre-drill, you don't need to use a special drillbit like you do for Confirmat. You do have to be careful using them in plywood though.
Fourth, use Glue Blocks. The reminder I got for doing this was from Bob Flexner, in this article. Glue blocks have been used forever, why not use them to upgrade Ikea furniture stiffness? Glue blocks for Ikea furniture will do (potentially) three things - give you more surface area to glue two elements that join at 90 degree angles, provide a 90 degree square for assembly and (if needed and is possible to do in a way that won't show) allows you something to anchor screws in. Yep, when you can, pre-drill and drive drywall screws through the chip board, into the hardwood blocks you've added, for more strength.
Finally, if you are stuck with an Ikea product that is falling apart, and wasn't doing exactly what you wanted to anyway - hack it! These folk repurpose Ikea stuff for some fun results. I especially like this one.
Oh, another good tip is that Ikea does sell replacement parts - handy if a leg or bit of hardware fell off during a move. If a panel was damaged, consider replacing it with plywood - same arguments as for using glue blocks, above.
To conclude, I still like used solid wood furniture better than new Ikea. But if you have to deal with it, I hope the above tips help.
Sunday, October 25, 2009
Saturday, October 10, 2009
"My favorite American Communists" (and their boxes)
Referring of course to The Shakers. I can't take credit for the phrase, that belongs to Roy Underhill, author of many books, host of the PBS show "The Woodwright's Shop" and now master of his own woodworking school. I wouldn't give up any important bits of anatomy, but I really would like to go to any class he teaches! (End of digression)
I don't want to get into who the Shakers were as a people / culture, I just want to gush about their legacy of fine craftsmanship. Many of the forms I first identified (in my naivete) as being "Craftsman" or "Arts and Crafts" belong to the Shakers. They were the first to eschew ornamentation of form for the higher beauty of function and simplicity. They made many fine things and there are plenty of books out there about their works. Today I just want to talk about Shaker Boxes.
In the days before Tupperware, Shaker oval boxes and other variations on this form were some of the best lightweight ways to store things. A couple of thin, steam bent hoops sized on forms, secured to themselves as well as their flat oval lid and bottom boards with wooden pegs and copper tacks and there you are: "green" biodegradable storage that can last forever, with care.
Pictured at the left is John Wilson with his work. He has the best website for all things related to making or buying modern Shaker Boxes. If you are interested in making these, his catalog is required reading. For one thing, I'm not sure you can buy the copper tacks anywhere else. "The copper tacks used in oval box construction are made on machines that date back to the 1800’s. Our machines were acquired from the W.W. Cross Nail Co. when they ceased tack manufacturing in 1991. We currently make nine sizes of tacks plus the ½” copper shoe peg used for securing top and bottom boards when copper is preferred in place of wood pegs." Shaker boxes range from 000 (tiny) to size 12, although I've seen pictures of larger coffee table sized boxes. Each size nests into the next larger size. Eventually I will try my hand at a stack of these.
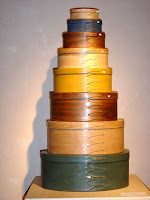
In the days before Tupperware, Shaker oval boxes and other variations on this form were some of the best lightweight ways to store things. A couple of thin, steam bent hoops sized on forms, secured to themselves as well as their flat oval lid and bottom boards with wooden pegs and copper tacks and there you are: "green" biodegradable storage that can last forever, with care.
Wednesday, October 7, 2009
November Wedding Garden Arbor #2
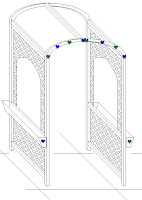
In thinking about this design, I think if I had the skills and right tools, I would make the Arbor frame out of powder coated welded steel for durability and to give it a more "airy" feeling & to allow it to survive outdoors longer. Vinyl instead of wood lattice was selected by the couple for its durability. But, wood for the frame is warmer to the touch and more relaxed than formal & it will be beautiful. (Fingers crossed)
Oh, in this Home Depot picture you can see what I was talking about regarding wood patches to tie the top and the sides together. I'm glad we can do without those!
Labels:
Arbor,
Flower Boxes,
Garden Arbor,
Home Depot,
Lattice,
sketchup,
Vinyl Lattice,
Wedding,
Wedding Arch
Tuesday, October 6, 2009
November Wedding Garden Arbor
Our only local cousins oldest son Jeremy is getting married to Natalia (who is already part of the family) in just less than one month! I asked them what they would like me to make for them as a gift and instead of some piece of indoor furniture, they came up with the idea of a garden arbor - that they will be married under! How fun is that? The only picture for this post is a simple illustration of the basic frame of the arbor / arch. Five feet wide and four feet deep, it will be the perfect size to frame the lovely couple and minister, and a garden bench afterward. The design is Jeremy and Natalia's - I just had to figure out how to fit the bits together.
Details of this Arbor: The arch joins the uprights smoothly, rather than with overhangs like some. As they are getting married outdoors, the arbor will disassemble into 3 pieces (top and two sides) for easy transport. The sides and top will be composed of lattice over the frame shown, with an arch-topped "window" in each side. The middle rail on each side will support a flowerbox, also decorated with hearts. The lowest side rail is slightly above the "feet" to keep it from ground contact. The top rails abutt the bottom rails of the arch.
I was looking at different ways of joining the arch to the sides and have seen a number of relatively simple ways, from overlapping wooden joining plates to metal straps. My first inclination was to join the pieces in some hidden fashion, both for appearance and to prevent places for the ubiquitous rain and dew to catch and aid in the decay of this structure. What I came up with is shown. The rails themselves will be joined by screws from the bottom side of the top side rail into the bottom of the bottom rails of the arch, so no wooden patch plates or Simpson Strong-ties will be needed. So a nice smooth appearance.
The fasteners are stainless steel, the lattice is vinyl and the wooden frame is treated cedar 2x2s, painted white. Exterior construction caulk to keep rain out of places it shouldn't be. The side flower boxes are cedar. Construction begins this upcoming Saturday.
Details of this Arbor: The arch joins the uprights smoothly, rather than with overhangs like some. As they are getting married outdoors, the arbor will disassemble into 3 pieces (top and two sides) for easy transport. The sides and top will be composed of lattice over the frame shown, with an arch-topped "window" in each side. The middle rail on each side will support a flowerbox, also decorated with hearts. The lowest side rail is slightly above the "feet" to keep it from ground contact. The top rails abutt the bottom rails of the arch.
I was looking at different ways of joining the arch to the sides and have seen a number of relatively simple ways, from overlapping wooden joining plates to metal straps. My first inclination was to join the pieces in some hidden fashion, both for appearance and to prevent places for the ubiquitous rain and dew to catch and aid in the decay of this structure. What I came up with is shown. The rails themselves will be joined by screws from the bottom side of the top side rail into the bottom of the bottom rails of the arch, so no wooden patch plates or Simpson Strong-ties will be needed. So a nice smooth appearance.
The fasteners are stainless steel, the lattice is vinyl and the wooden frame is treated cedar 2x2s, painted white. Exterior construction caulk to keep rain out of places it shouldn't be. The side flower boxes are cedar. Construction begins this upcoming Saturday.
Labels:
Garden Arbor,
Hearts,
Wedding,
Wedding Arch
Subscribe to:
Posts (Atom)