My friends Donna and Mike have been making incremental improvements to their 40 year old house ever since they bought it. Their latest project was to replace the dark Oak parquet floor in their entry and first floor hallway and to replace the Linoleum in their kitchen all with Oak strip flooring to match their dining room and living room. To address wear concerns, they opted for a tiled entry, placed as a inlay with oak flooring around it.
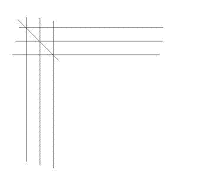
One of the questions was how to best frame the area where the tile would go / how to make the transition. The initial thought was to make a mitered corner two-strip-wide border, to effectively picture frame the tile. As I was drawing out the lines for this framing / showing how it would look on the membrane paper that goes between the flooring and the subfloor, Donna came through and saw lines marked on the paper like this and said "how pretty!" She wasn't seeing what Mike and I were seeing - she saw corner blocks with angled cuts, out of contrasting wood, where we saw mitered corners & continuation lines to mark out the miter. So, as a trial, we cut small square blocks of Oak from the scrap offcuts of the flooring and used dark markers to simulate the contrasting colors of an accent wood like Walnut.
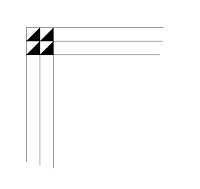
Even with the blocks rotated into the kite pattern you see here at the left, it wasn't exactly what they were looking for, but they still liked the idea of some form of contrasting wood detail around the entry. What they decided on was solid squares of Walnut, 2 per corner.
Making the little Walnut blocks was interesting - 2 sides tongue, 2 sides groove (to tie in with the tongues and grooves of the rest of the flooring) and I tried to gang cut them on the table saw as much as possible & then cut the joining tongues apart as the last operation. Still, getting the blocks sized correctly took a lot of time! Cutting the blocks without tongues or grooves would have taken just a few minutes instead of the few hours. But, hopefully the floor will be more solid because of the pains we took. I made a total of 14 blocks out of a small board of figured Walnut I had been hoarding and they selected their 8 favorites for appearance / grain direction, etc. And the results look like this:
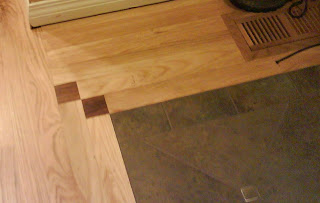
At the point this picture was taken everything is finished except for the molding. The Oak register covers look great and Donna and Mike have a seamless Oak floor for much of the first floor. The flooring matched very nicely with the original Oak after it was sanded and finished as the one floor it now is. They selected
Swedish Finish for its durability. It really looks nice. Oh, in the tile work, note the stainless steel accent tile in the lower right of this picture. They used a similar tile pattern to cover the bricks of their living room fireplace surround - it really helps tie everything together & looks great. So, I suppose the lesson in this is that it really helps to have multiple sets of eyes on a project, before you start cutting wood. Without Donna's perception, this would have been a much plainer floor!