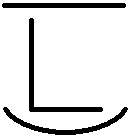
This post is all about signing and dating work. Typically, I don't - mostly I don't think that my work / most work merits a signature. I feel like that is something reserved for artists / things of artistic merit rather than the ordinary or utilitarian. But, as much of what I do is for family, I've given serious consideration to marking pieces for the benefit of future generations. (Lofty dreams, hoping that your hand-crafted what-not isn't put in the dump after whoever you made it for is done with it!) But, leaving that behind for now, there are a few ways people brand their items:
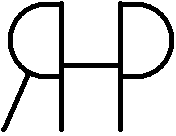
The easiest is to simply use an indelible / laundry marker to write on some inconspicuous place before applying finish. Any good permanent marker like a Sharpie would work. You may want to put on a thin coat of finish first, so the marker doesn't "bleed" quite so much, and then finish as usual over it. Another is buy a wooden or
metal "mark" that you would buy especially for the purpose - most are round and easily inset into your project.
Rockler and many other companies offer
woodburning brands that you can customize - some with your name, some that are just a logo, even just initials. I've seen them offered with and without their own heat, so some are truly like a branding iron, while most are like large electric soldering irons. They even offer a date attachment that you can change (buy a new one) each year - but it is so expensive you may as well buy a whole new brand. Well, some of the graphic brands are more expensive, shrug, may be worth it for those.
Some use the right size
forstner bit and drill a shallow recess and epoxy in a coin with the current year. I like this because it gives a solid date that can survive refinishing if need. Whenever you embed a coin though, you wonder if some 10 yo is going to dig it out eventually - either for his collection, or to put in a gumball machine.
Decals and stickers are another option and have been used by professionals and amateurs for many years as well - you can now make your own decals easily using a desktop inkjet printer.
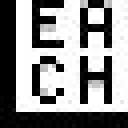
I "Branded" this Blog by making a "Leach" icon that is simply a large "L" cradling the letters e,a,c,h. which arose from my interest in creating a furniture brand. If I was going to use this as a basis for a
decal, the "L" would be a try-square. The top two brands pictured
are real cattle brands from our family history / background in farming and ranching. The first is
Bar Lazy L ( (the horizontal top line over an L over a rocker) which was our Paternal Grandfather's brand. The second brand was our Maternal Grandfather's initials, with the first initial reversed for balance, probably the same as his monogram.
Anywho, no decisions yet on a brand for me. We've done a few "branded" projects - one by putting a hand written piece of paper into a hollow spot in the project (I like that, and will do it again) before sealing it closed and another by signing in ball-point pen (although a laundry marker would have been much better) and finishing over that.
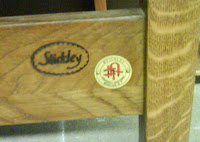
I'm leaning towards a wood-burned brand coupled with an epoxied U.S. dime. Both can survive most any kind of abuse / refinishing / painting. That combination seems busy /overdone somehow - but I don't want to make a new brand for each new year. The
modern Stickley company uses a wood burned brand and a brad-fastened metal mark that has elements from the original logos. The brand pictured is on a twin bedframe headboard - this mark would be hidden by boxspring. This is another combination that can survive refinishing. I want something smaller though, so that I can mark smaller projects as well as the large. Any thoughts or suggestions appreciated!