If you cut through your cord, you could simply add a new plug to the existing cord at the break, without the need for disassembling the tool itself - assuming that you can live with a shorter power cord. If this is the direction you want to go, there are a great variety of tool plugs that you can get.
A lot of contractors like short cords with twist-lock plugs - especially for roof framing where losing connection between a framing saw and the extension cord can not only mean time lost, but can be a hazard to anyone below. Personally, I favor the standard "Edison" standard wall-plug connectors that most tools come with by default, as rewiring or using adaptors can be an expensive proposition and I'm not on a roof with a saw all that often.
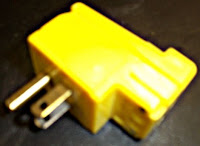
Another alternative to buying a replacement cord is to go the other way - use the piece of severed cord with molded plug attached (or whatever clean length of cord there is between the plug and the break or abrasion) and replace the "stub" as in the above Fine Homebuilding article. You may have to put your own connectors on it, or use a soldering iron to tin the leads, but it is a darn sight cheaper than buying a new cord from the manufacturer. Actually, I've only bought a new replacement power cable once - and that was because the strain relief was ruined, and the new cord came with one specific to the tool which was molded on to the cord rather than a separate part. Even if you aren't busily ruining power cords yourself, the most common defect you run into when buying a used power tool is a bad cord - generally repaired with miles of black electrical tape! Getting comfortable making this type of repair will keep you a good deal safer and good tools out of metal recycling bins.
1 comment:
Good information. I like the reuse rather than put in a land fill angle, good advice.
Cheers!
Post a Comment